Schematic Diagram of double-control with double-computer
The electric control system is consisted of two (sets of) computers, among which, one is the computer for major production control and the other is the standby computer for management. The computer for major production control performs sampling, calculating, comparing, processing of the external signals and the control of input/output command, which realizes the control over the external executors, manages starting/stopping of mechanical-electrical doors of peripheral hoppers, and therefore performs effectively the control of automatic production. The standby computer for management is for keeping the document of routine production and management, which may be used either as monitor or as server to constitute a LAN with other computers to realize the share of resource. In case the computer for major production control is out of order, the standby computer for management may take over the control operation without artificial intervention, which realizes the unceasing operation of the electric control system without any trouble.
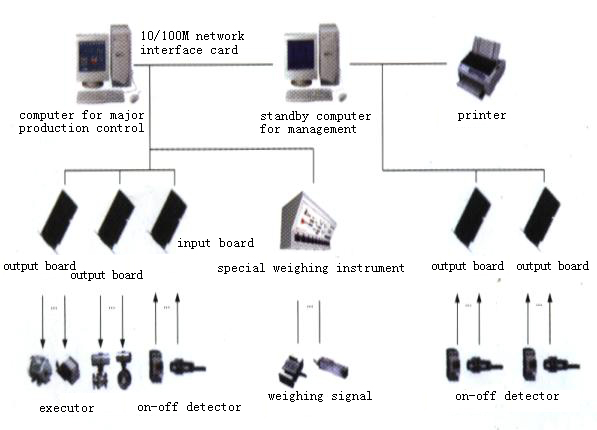
The electric control system is consisted of a (set of) computer plus PLC mode to realize effective control over two sets of equipments (in switching manner). The system performs sampling, calculating, comparing, processing of the external signals and the control of input/output command, which realizes the control over the external executors, manages starting/stopping of mechanical-electrical doors of peripheral hoppers, and therefore performs effective control of automatic production. In case an agitator is out of order, the other agitator may be started automatically to guarantee the unceasing operation of the machinery without any trouble.
Electronic components are selected from such manufacturers as Schneider, Siemens, LG, Omron, Meanwell, Weidmuller, Toledo and so on, which guarantees effectively the stability of electric control system.
Concrete Mixing Control System
The control system adopts Windows as the operation platform, takes the production control as its key task, and adopts such control manner as "industrial control computer + industrial programmable controller "or" industrial control computer + weighing instrument + control board". . It is an automatic control system of high stability, high real time capability and high intelligence. The control program of the upper computer of the industrial control integrates the most advanced concept of simulation neural network model in industrial control at home and abroad, i.e. the program has simulation function, real time state control, self-execution and self-study on real time information feedback on the working state of the equipment. The output signal state of the industrial programmable controller is decided by the set functions of the control program of the upper computer, to control the opening and closing of each hopper gate and to control the start-up and shut off of the motor, to realize auto control production.
The newest design concept of the program of control system
1.The function of the task priority of the task list: Considering that the production formulation may be changed frequently on the field, a queue of multiple different formulations may be established before or during the production by using this function, so that the production may be switched continuously among them to save the production time.
2.The function of delay weighing compare and steady weighing control: In dynamic weighing, the weight of materials may be influenced by impulse, which may result in false signal given by the sensor. But this system adopts the function of delay weighing compare and steady weighing control, which is able to control weighing accuracy effectively in dynamic weighing.
3.The function of digital filtering: It has tuning effect on frequent small variation of signals due to the temperature drift, auto oscillation, pressure sensitive and signal source interference of the sensors.
4.Pause function of control flow: it is able to meet the requirement of pause function of control flow due to working needs in continuous production.
4.1 Weighing pause: under semi-(full) auto state, it is able to pause all the weighing operations. After reset, it is able to recover normal working state.
4.2 Material-feeding pause: under semi-(full) auto state, it is able to pause the feeding of (transitional cabin, cement, water or additives). After reset, it is able to recover normal working state
4.3 Discharging pause: under semi-(full) auto state, it is able to pause discharging. If this function has been set on in discharging, please shut off the discharging gate first and remain current discharging timing. It will recover to normal working state after rese
5.Weighing control mode of quick/slow valve: based on the control philosophy of coarse/fine weighing in the mixer industry, it is an adjustable control mode relying on drop height and drop timing according to the sizes of materials.
6.The function of auto calibration of zero: in consideration of the left materials on the weigher in actual production, this function ensures accurate weighing through the effective calibration.
7.The function of auto calibration of drop height: in consideration of the uncertainty of drop height in actual production, this function is optional to realize effective data analysis and intelligent auto control adjustment to ensure accurate weighing.
8.The function of intelligent timing control;
9.The function of intelligent information alarm: real time indications on the running state of the system are given and false operations of the user are explained.
10.The function of the flow memory control: the stability and intelligence of the system control can be realized through formed flow memory control, so as to reach the philosophy of actual auto control.
11.Function of the operation log: it may register effectively each operation procedure after operators have logged in the control system, which performs effectively the operation management in the manner of black box.
12. Function of stepwise feeding and separately mixing: this function may be utilized based on the process requirements of high performance concrete with high iron content.
13.Powerful intelligent report form management
Production report forms for all customers/recipes.
Transportation report forms for all vehicles.
Daily, monthly and annual report forms for material consumptions.
Daily, monthly and annual report forms for production capacity.
Daily, monthly and annual report forms for transportation volume.
Management of stock and consumption of powder stuff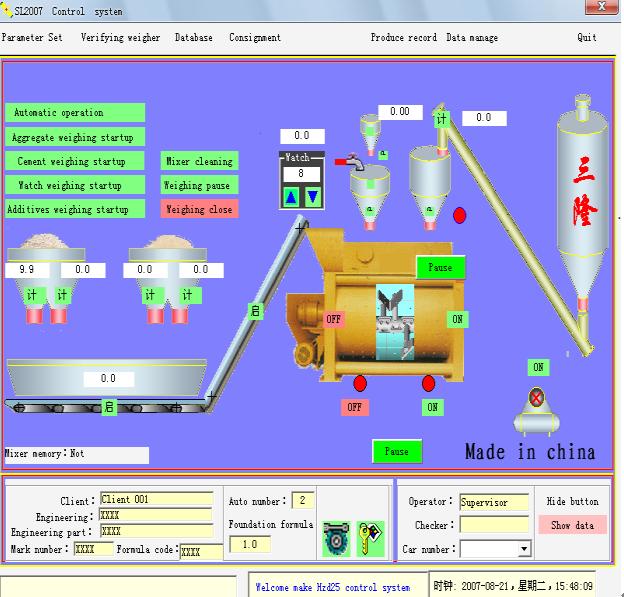
Friendly man-machine interface, characterized by high efficiency and real time, may present the production status on the field to us in the manner of cartoon or data, judge and analyze the operation condition on the field intelligently, and implement strictly the humanistic automatic control of production.
It is available for various settings of material batching, material feeding, emptying value, material feeding time, and creation and read-in of formula upon field production requirement at any time.
It is available for settings for rough weighing value of various material, control model, auto weighing balance, auto weighing reserve, auto gap correction and auto zero tracing upon field production requirement at any time;
Powder Inventory and Consumption Management:
To solve the problems of incorrect inventory measurement of powder material by material level detector, the control function of this system can effectively and automatically calculate the amount of each inventory and generate the total amount; Then, calculate powder material consumption of each tray to generate effective total powder material consumption, so as to achieve a series of in-stock, consumption and inventory data to assist the field production management with data and chart;
In light of the technical requirement of stepwise feeding and separately mixing in production of high performance concrete for high-speed railway, through the intelligent material feeding sequence control option : The feeding of fine aggregate, rough aggregate and powder material can be set as the 1st or 3rd feeding; The feeding of water can be set as the 1st, 2nd and 4th feeding or fed by amount; The feeding of additives can be set as the 1st, 2nd and 4th feeding; With the successful experience in high-speed railway construction, the improving functions of our equipment may completely meet the construction requirements of high-speed railway;
Digital wave filter function: It is of great effect in rectifying the frequent signal fluctuation in small area caused by the temperature drift, self-vibration, voltage sensitivity, stimulation and interfered signal source of the sensor;
Function of delivery order: base on the components of production report forms, such as the material receiving unit and project name, collect the data of delivery order of supply amount for each vehicle and each tray by sort. It allows us to change the data of delivery order to satisfy the different requirements of different area to the delivery order.
Function of the operation log: it may register effectively each operation procedure after operators have logged in the control system, which performs effectively the operation management in the manner of black box..
Production report table can provide the specific data query for name of client, name of project, part of construction, concrete grade, formula used, date (it is available for annual report, monthly report and daily report) which are accurate to a certain time period, and the sorted query for total production volume, total transportation volume and the total transportation of each vehicle according to the field use requirements of clients;